Dry goods | oscilloscope probe all sorts of function and working principle – FAST TURN CHIP
Because of the existence of the probe, the scope of application of the oscilloscope is expanded, so that the oscilloscope can test and analyze the electronic circuit under test online, as shown below:
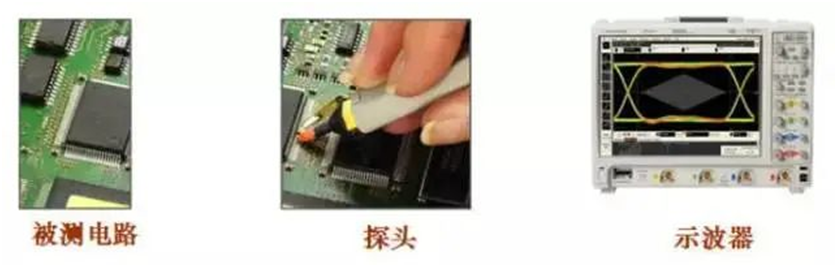
The selection and use of probes need to consider the following two aspects:
One: because the probe has a load effect, the probe will directly affect the measured signal and the measured circuit;
Second: the probe is a part of the whole oscilloscope measurement system, will directly affect the instrument signal fidelity and test results.
Probe load effect
When the probe detects the circuit under test, the probe becomes part of the circuit under test. The load effect of the probe includes the following three parts:
- 1. Resistive load effect;
- 2.Capacitive load effect;
- 3. Perceptual load effect.
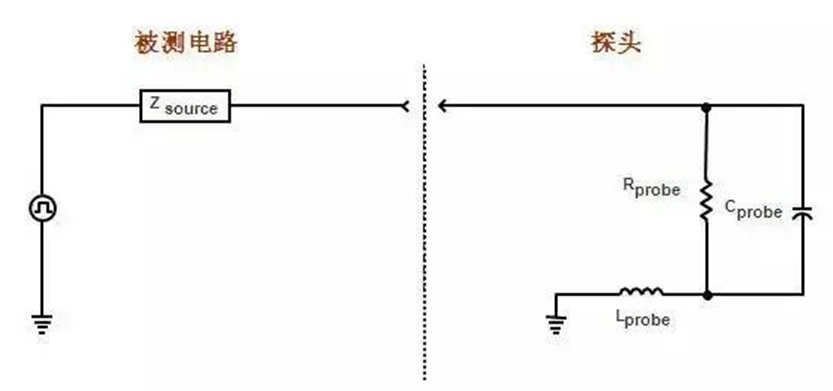
A resistive load is equivalent to a resistor in parallel on the measured circuit, which has a partial pressure effect on the measured signal and affects the amplitude and DC bias of the measured signal. Sometimes, when a probe is added, a faulty circuit may become normal. Generally recommended probe resistance R> 10 times the measured source resistance to maintain an amplitude error of less than 10%.
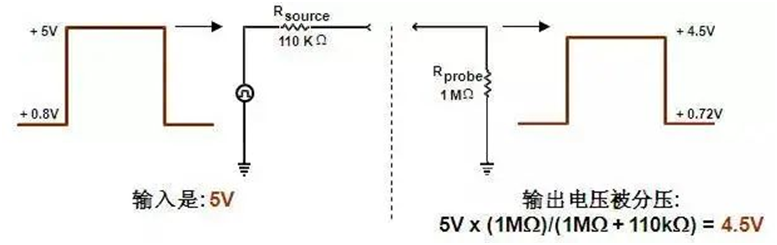
Capacitive load is equivalent to a capacitor in parallel on the measured circuit, which has a filtering effect on the measured signal, affecting the rise and fall time of the measured signal, affecting the transmission delay, and affecting the bandwidth of the transmission interconnection channel. Sometimes, when the probe is added, the faulty circuit becomes normal, and this capacitance effect plays a key role. It is generally recommended to use a probe with as little capacitive load as possible to reduce the impact on the measured signal edge.
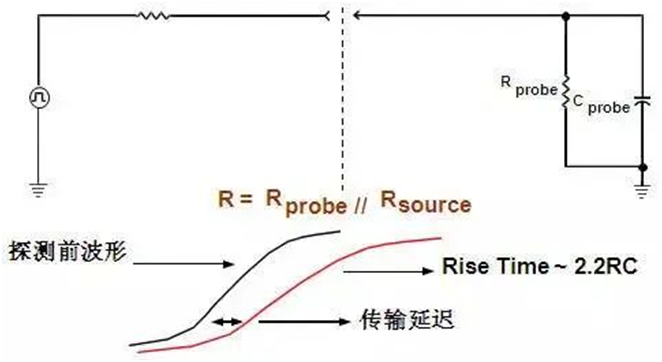
The inductive load is derived from the inductive effect of the probe’s ground wire, which resonates with the capacitive and resistive loads to cause ringing on the displayed signal. If a ringing signal is displayed, check whether the ringing is caused by the real signal or the ground cable. Use the shortest ground cable to confirm the ringing. Generally, it is recommended to use the shortest ground wire, with inductance =1nH/mm.
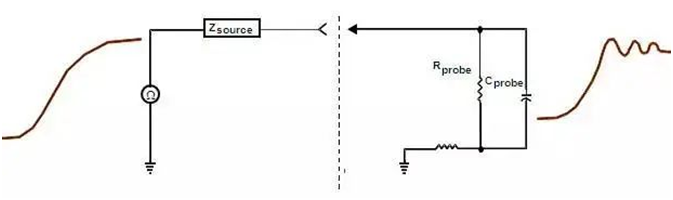
Type of probe
Oscilloscope probe big aspects can be divided into: passive probe and active probe two categories. Passive active, as the name implies, is the need to power the probe.
The passive probe is subdivided as follows:
1. Low resistance resistor pressure probe;
2. High resistance passive probe with compensation (the most commonly used passive probe);
3. High pressure probe.
The active probe is subdivided as follows:
1. Single-end active probe;
2. Differential probe;
3. Current probe.
The most commonly used high resistance passive probe and active probe simple comparison is as follows:
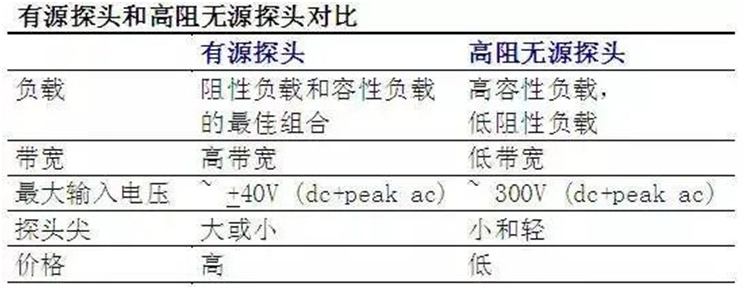
Low resistance resistor divider probe with low capacitive load (& LT; 1pF), higher bandwidth (> 1.5ghz), lower price, but the resistance load is very large, generally only 500ohm or 1Kohm, so it is only suitable for testing circuits with low source impedance, or circuits that only focus on time parameter testing.
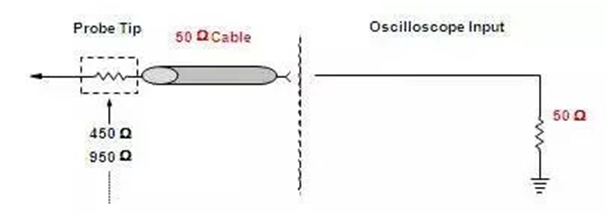
The high resistance passive probe with compensation is the most commonly used passive probe, which is the standard probe of the general oscilloscope. The high resistance passive probe with compensation has a higher input resistance (generally more than 1Mohm), adjustable compensation capacitor to match the oscilloscope input, has a higher dynamic range, can test a larger signal (dozens of more), the price is also lower. However, it is unknown that the input capacitor is too large (generally more than 10PF) and the bandwidth is low (generally less than 500MHz).
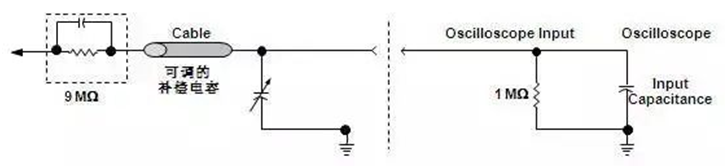
High resistance passive probe with compensation has a compensation capacitor, when connected to the oscilloscope, generally need to adjust the capacitance value (need to use the probe with a small screwdriver to adjust the probe to the oscilloscope compensation output test position), to match the oscilloscope input capacitance, to eliminate low frequency or high frequency gain. In the presence of high or low frequency gain on the left side of the figure below, the adjusted compensation signal shows the waveform as shown on the right side of the figure below.
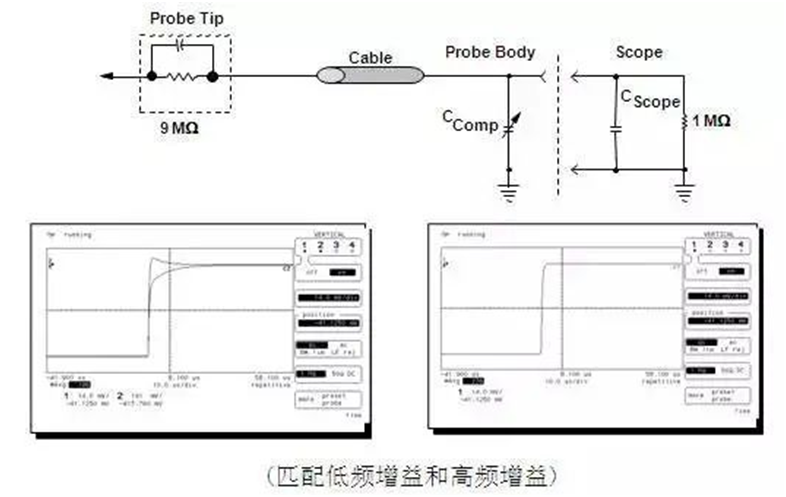
The high voltage probe is a passive probe with compensation based on increasing the input resistance, so that the attenuation increases (such as: 100:1 or 1000:1, etc.). Because of the need to use high pressure components, the physical size of the high pressure probe is generally larger.
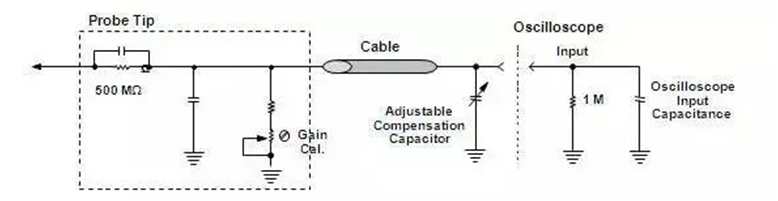
Active probe
Let’s first observe the effect of testing the 1ns rise time step signal with a 600MHz passive probe and a 1.5GHz active probe. The pulse generator is used to generate a 1ns step signal. After passing the test fixture, the SMA cable is connected directly to an oscilloscope with a 1.5GHz bandwidth. The oscilloscope will display a waveform (the blue signal shown below) and store this waveform as a reference waveform. Then use the probe point measurement test fixture to detect the measured signal, through the SMA directly connected waveform because of the impact of the probe load into yellow waveform, probe channel display is green waveform. Then the rise time is measured respectively, and the effect of passive probe and active probe on high speed signal can be seen.
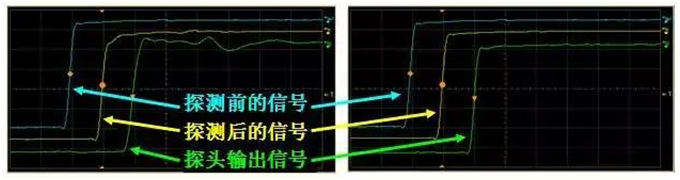
The specific test results are as follows:
Using 1165A 600MHz passive probe, using crocodile mouth ground wire: affected by the probe load, the rise time becomes: 1.9ns; The waveform displayed by the probe channel is ringing, and the rising time is 1.85ns;
Use 1156A 1.5ghz active probe, use 5cm ground wire: less affected by probe load, rise time is still: 1ns; The waveform displayed by the probe channel is consistent with the original signal, and the rise time is still: 1ns.
The single-end active probe structure is shown below, and an amplifier is used to achieve the purpose of impedance conversion. The single-ended active probe has a high input impedance (generally up to 100Kohm or more) and a small input capacitance (generally less than 1PF). After being connected to an oscilloscope through the probe amplifier, the oscilloscope must use 50Ohm input impedance.
The active probe has a wide width (up to 30GHz now), but the load is small, but the price is relatively high (generally, each probe reaches about 10% of the price of the same bandwidth oscilloscope), and the dynamic range is small (this needs to be paid attention to, because the signal exceeding the dynamic range of the probe can not be tested correctly. General dynamic range of about 5V), more fragile, use need to be careful.
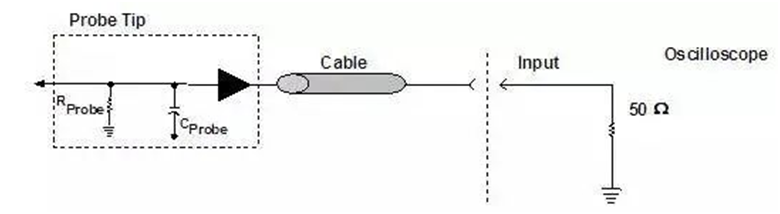
Differential probe structure is shown as follows. Differential amplifier is used to achieve the purpose of impedance conversion. The differential probe has a high input impedance (generally more than 50Kohm) and a small input capacitance (generally less than 1PF). After connecting to an oscilloscope through a differential probe amplifier, the oscilloscope must use 50Ohm input impedance.
Differential probe very wide bandwidth (up to 30 GHZ) now, the load is very small, with high common mode rejection ratio, but the price is relatively high (usually every oscilloscope probe to reach the same bandwidth prices by about 10%), the dynamic range is small (the need to pay attention to, because more than the probe signal dynamic range, can not correctly test. General dynamic range of 3V or so), more fragile, use need to be careful.
Differential probes are suitable for high-speed differential signal testing (testing without grounding), suitable for amplifier testing, power testing, virtual ground testing and other applications.
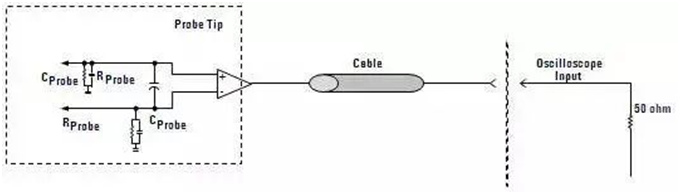
Current probe is also active probe, using Hall sensor and induction coil to achieve DC and AC current measurement. The current probe converts the current signal into voltage signal, and the oscilloscope collects voltage signal and displays the current signal. The current probe can test the current from tens of milliamps to hundreds of amperes, and it needs to lead out the current line when using it (the current probe is to clip the wire in the middle for testing, which will not affect the circuit to be tested). How the current probe works when testing DC and low-frequency AC: When the current clamp is closed, enclosing a current conductor in the center, a magnetic field will appear accordingly. These magnetic fields deflect electrons within the Hall sensor, generating an electromotive force at the output of the Hall sensor. Based on this electromotive force, the current probe generates a reverse (compensating) current to the current probe’s coil, keeping the magnetic field in the current clamp to zero to prevent saturation. The current probe measures the actual current based on the reverse current. With this method, it is possible to measure high currents very linearly, including mixed currents.
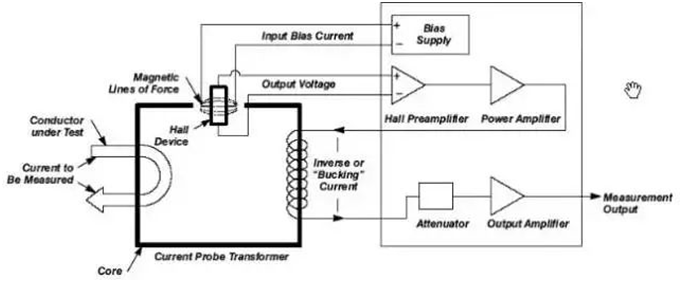
Working principle of current probe when testing high frequency:
With the increase of measured current frequency, hall effect gradually weakened, when measuring a high frequency AC current without DC component, most of it is through the strength of the magnetic field directly induced to the current probe coil. At this point, the probe acts like a current transformer. The current probe directly measures the induced current, not the compensation current, and the output of the amplifier provides a low-impedance grounding loop to the coil.
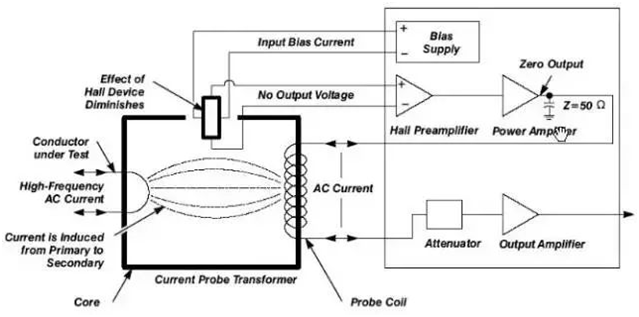
Working principle of current probe in cross region:
When the current probe operates in the high and low frequency crossover region of 20KHz, part of the measurement is achieved through the Hall sensor and the other part is achieved through the coil.
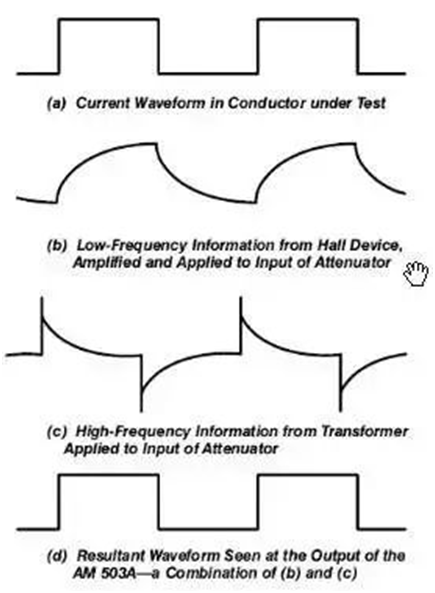
Active probe accessory
Modern high-bandwidth active probes are designed separately, that is, the probe amplifier is separated from the probe accessories. The benefits of this design are:
1. Support more probe accessories, making the detection more flexible;
2. Protection investment, the most expensive is the probe amplifier (a probe amplifier can support a variety of detection methods, previously needed several probes to achieve); At the same time, the probe accessories protect the probe amplifier (even if the probe accessories are damaged, the price is relatively cheap);
3. This design method is easy to achieve high bandwidth.
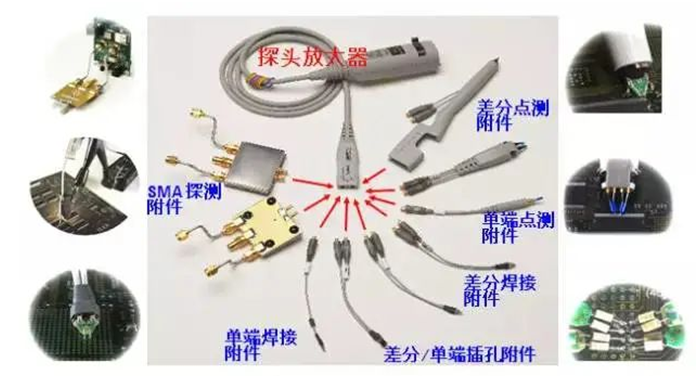
These probe accessories mainly include the following:
1. Point detection head accessories (including: single end detection and differential point detection);
2. Welding probe accessories (including: single-end welding and differential welding, separated ZIF welding);
3. Jack probe accessories;
4. Differential SMA probe accessories (oscilloscopes generally directly support SMA connection, but if the measured signal needs to pull up such as HDMI, SMA probe accessories must be used).
The circuit structure of the probe accessory is shown as follows:
1. There will be a pair of damping resistors (generally 82Ohm) at the tip of the probe attachment, which is used to eliminate the resonance effect of the inductance at the tip of the probe attachment;
2. Behind the tip part of the probe is the resistance of 25Kohm, which determines the input impedance of the probe (DC input impedance namely resistance: single-end 25Kohm, differential 50Kohm). This resistance makes the power of the measured signal transmitted to the probe amplifier part is very small, so as not to have a great impact on the measured signal.
Behind Kohm’s resistor is the coaxial line section, which is responsible for transmitting small signals to the amplifier. The length of the transmission line can be very long or very short, with an attenuator or a coupling capacitor in the middle.
4. Coaxial transmission lines are connected to amplifiers that are 50ohm matched (differential 100ohm matched).
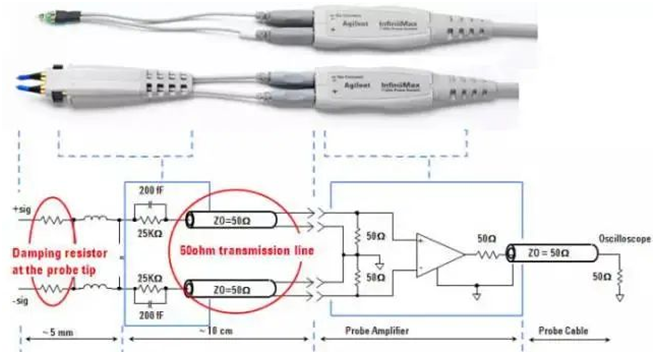
In order to maintain the accuracy of the active probe, the probe amplifier needs to work in a constant temperature state, so the probe amplifier can not be placed in the high and low temperature chamber for the test of the circuit board under high and low temperature environment. It can be seen from the probe accessory structure that the length of the 50ohm transmission line in the middle does not affect the detection, so you can use a very long coaxial cable or extended coaxial cable, so that the coaxial cable into the high and low temperature box for high and low temperature into the circuit board under test.
Probe and accessory accuracy verification
- Figure A shows the test results using 12GHz 1169A differential probe and N5381A 12GHz welded probe attachment, which almost completely reproduce the measured signal;
- Figure B shows the test results of the passive probe with 500MHz, and the displayed signal is completely distorted.
- Figure C shows the test results of 12GHz 1169A differential probe and a long test lead, showing a large overshoot.
- Figure D shows the test results using a 4GHz 1158A single-end probe and a long test lead. The signal displayed is almost a sine wave with large distortion.
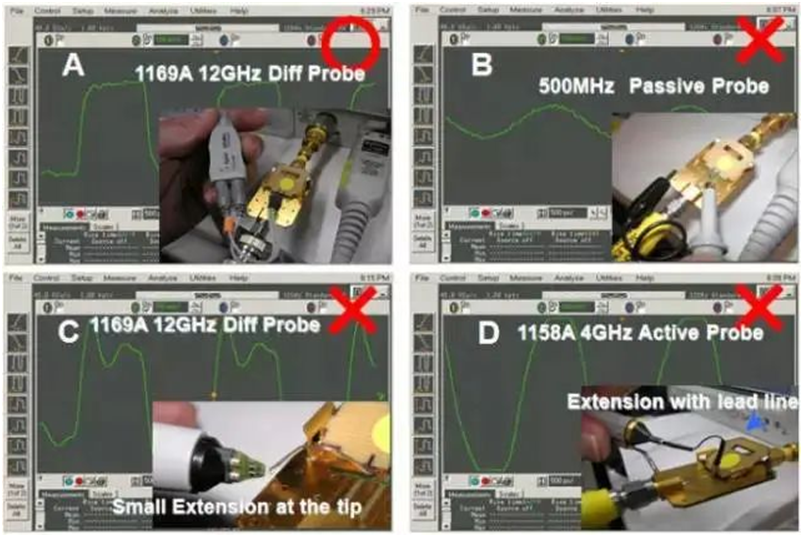
It can be seen from the figure that the probe and probe accessories have a great influence on the test accuracy, which is one of the contents we should pay attention to when testing high-speed signals. So how do we verify the probe and probe accessories?
A pulse code generator (e.g. 81134A, 3.35ghz rate, 60ps edge pulse code generator) is required to verify the probe and probe accessories. If the oscilloscope has a high-speed signal output function, the auxiliary output port of the oscilloscope can also be used to replace the pulse code generator (e.g. Infiniium oscilloscope AUX OUT port can emit a high-speed clock: 456MHz frequency, about 65ps edge).
In addition, coaxial cables and test fixtures are required (probe calibration jigs with Infiniium oscilloscopes can be used as probe and probe attachment verification test jigs). The outer surface of the test fixture is Ground, and the inner wiring is Signal, as shown below. When in use, connect one end to AUX OUT port of auxiliary output of pulse code generator or oscilloscope through coaxial cable, and connect the other end to channel 1 of oscilloscope through adapter.
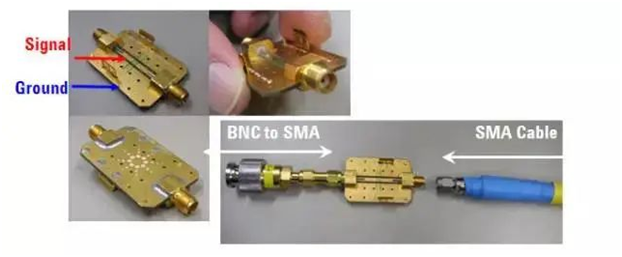
The verified probe is then connected to channel 2. The probe can contact the signal and ground of the test fixture through the probe attachment (if it is a differential probe, connect the + end to the signal line of the test fixture and connect the -end to the ground of the test fixture).
1. If the probe does not touch the signal line, an original waveform will appear on the screen and be stored as a reference waveform;
2. When the probe is used to detect the signal line, the waveform of channel 1 will change, and the waveform after the change is the measured signal influenced by the probe and probe accessories;
3. At this time, a waveform will appear in the channel 2 connecting the probe, which is the waveform measured by the probe;
4. By comparing the reference waveform, the waveform of channel 1, and the waveform of channel 2 connected with the probe, you can intuitively see or read the difference between the three through the test parameters, you can verify the influence of the probe and probe accessories.
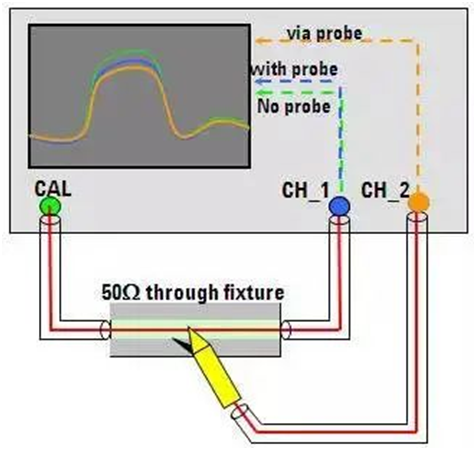
Below is an example of actual verification, the figure A oscilloscope AUX OUT through coaxial cable to connect to the test fixture, the other end of the test fixture by SMA – PBNC adapter connected to A channel of oscilloscope (this case is connected to the channel 3), the probe is connected to channel 1, adjust the waveform on the screen, at this time makes A edge step waveform, As shown in FIG. C, and save this waveform as the reference waveform. As shown in figure B in the validation of probes and accessories on the spot measurement to the test fixture, as shown in figure D, screen 3 waveform, the blue is a reference waveform, the green is affected by the probe after the measured waveforms, yellow is the probe, the wave form by test rise time parameters, overshoot parameters, etc., to confirm the performance of the probe and the probe attachment.
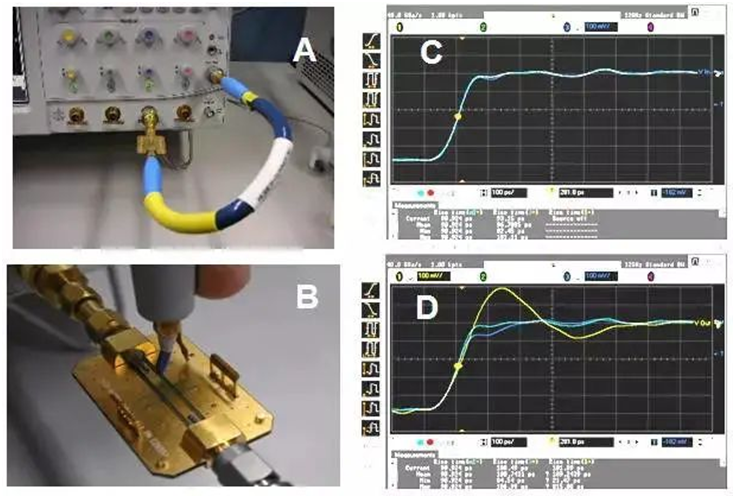
About Electronic components distributor FAST TURN CHIP
FAST TURN CHIP is a B2B electronic contract manufacturer with sourcing points for electronic components worldwide. We can find and source hybrid electronic components and ics at the lowest price and meet unique customer needs. No matter what components you want, no matter how many, you can buy from Cocreate At a reasonable price and with traceable quality.
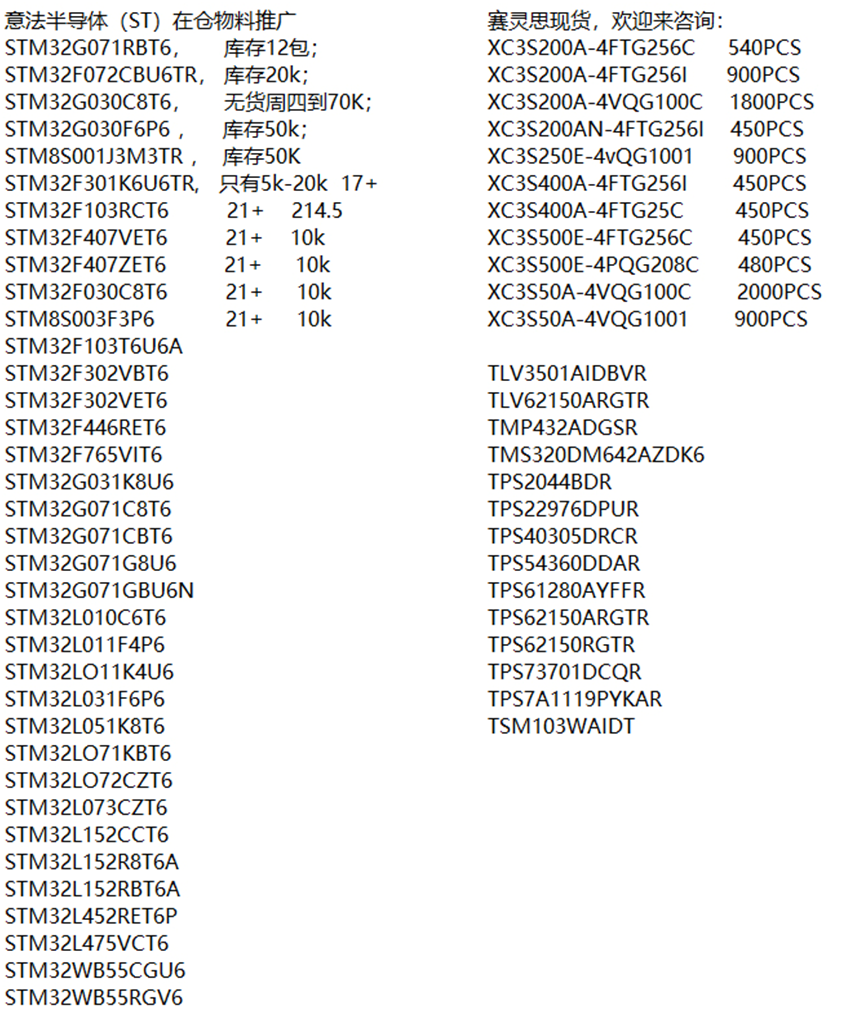