With the rapid development of information technology, the demand for electronic components in our country has gradually increased, and electronic components have gradually developed towards thinner, intelligent, integrated, and miniaturized trends, but this has also become an obstacle to the detection of electronic components , Which greatly limits the improvement of the mass production efficiency and product quality of the enterprise. Therefore, CCD visual inspection technology is needed to replace manual labor and traditional inspection methods through non-contact, damage-free, high-precision, and high-efficiency real-time inspection methods, so as to improve the productivity and product quality of enterprises.
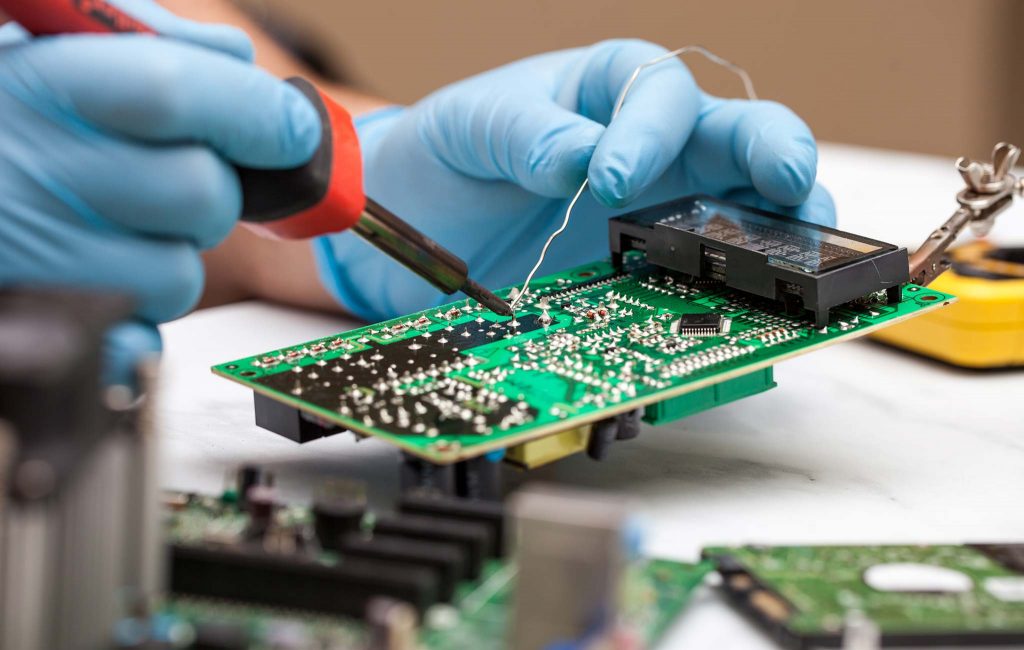
Advantages of CCD visual inspection:
1. Higher efficiency: manual detection is inefficient. Machine vision inspection speed is much faster, it can inspect hundreds or even thousands of components per minute, and it can work continuously for 24 hours.
2. Higher accuracy: Human eyes are limited by physical conditions, and are also affected by subjectivity, physical energy and other factors, and accuracy cannot be guaranteed. The machine is not subject to subjective control. As long as there is no difference in parameter settings, multiple machines with the same configuration can guarantee the same accuracy.
3. Lower overall cost: The machine is more effective than manual inspection, and it can store various types of product inspection process parameters, and only need to be recalled for future use. In the long run, the cost of machine vision inspection is lower.
4. Information integration: Machine vision inspection can measure multiple technical parameters at one time through the multi-station measurement method, such as the contour, size, appearance defect and product height of the product to be inspected.
5. Digital statistical management: measure data and generate reports after measurement, without manually adding them one by one.
6. Applicable to dangerous detection environments: the machine can complete the detection work well in harsh and dangerous environments, as well as in occasions where human vision is difficult to meet the needs.
7. No contact damage to the product: Machine vision does not need to touch the workpiece during the process of detecting the workpiece, and will not cause contact damage to the workpiece. Manual inspection must perform contact inspection on the workpiece, which is prone to contact damage.
8. More objective and stable: In the process of manual testing, the test results will be affected by factors such as personal standards, emotions, and energy. The machine strictly follows the set standards, and the test results are more objective, reliable and stable.
9. Avoid secondary pollution: manual operation sometimes brings uncertain sources of pollution, thereby contaminating workpieces.
10. Simple maintenance: low technical requirements for operators, long service life and other advantages.
Generally speaking, machine vision inspection has the characteristics of objectivity, non-contact and high precision compared with manual inspection. Especially in the field of industrial production, it has strong application value in repetitive and mechanical work, which not only ensures the stability of product quality, but also improves product competitiveness.